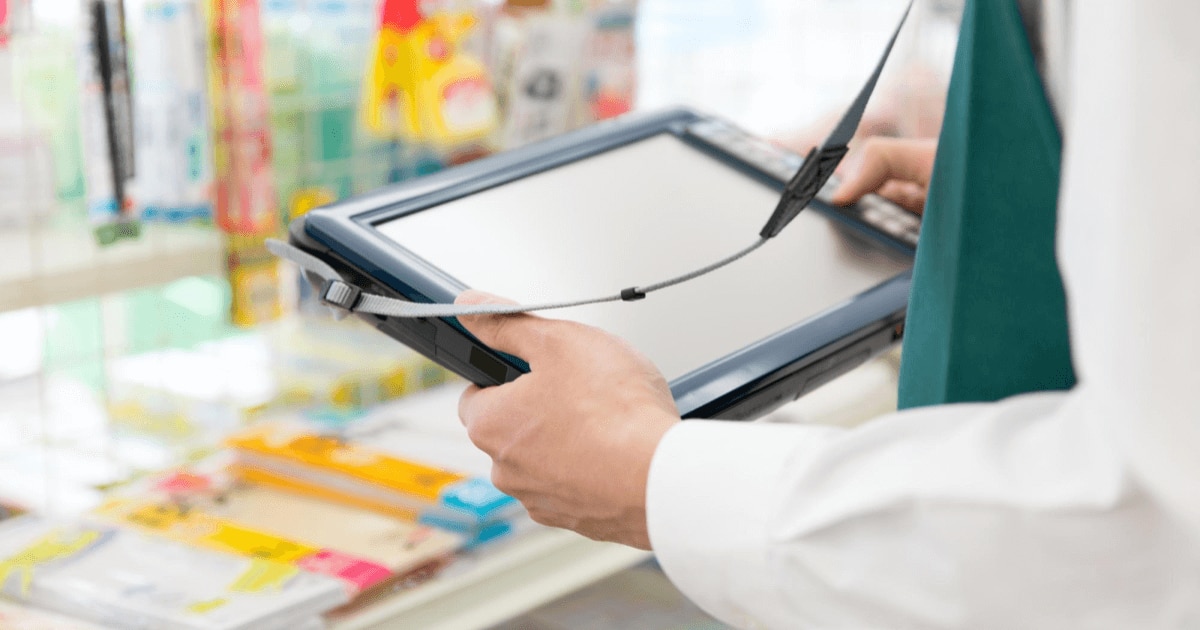
発注点を計算して在庫を適正化! 算出方法や管理のポイントを解説
在庫管理を行ううえで、欠品や余剰在庫を防ぐためには適切な発注タイミングを計算して見極めることが重要です。
発注を行うタイミングを“発注点”と呼び、在庫が一定数を下回った場合に発注をかける基準を指します。この発注点は、計算によって算出できます。
しかし、発注点を設けていない現場では、「担当者の勘によって発注が行われており、対応が属人化している」「発注の漏れや遅れが発生している」などのケースも少なくありません。また、発注点を設けていても、計算方法を見直したい方もいるのではないでしょうか。
この記事では、発注方式の種類や在庫の最適化を図るための発注点の計算方法、発注業務を効率化するシステムについて解説します。
▼こちらもおすすめ:在庫管理業務でお悩みの方に
目次[非表示]
- 1.発注方式の種類
- 2.発注点の計算方法
- 3.発注点を管理する際の3つのポイント
- 3.1.1.在庫数を正確に把握する
- 3.2.2.需要状況に応じて発注点を見直す
- 3.3.3.システムを活用する
- 4.受発注システム活用で在庫管理を効率化!
発注方式の種類
発注方式は、定量発注方式と定期発注方式の2種類に分けられます。
▼発注方式の種類
種類 |
詳細 |
定量発注方式 |
在庫数の基準を定めて、一定数を下回ったときに発注する |
定期発注方式 |
設定した期間ごとに必要量を発注する |
定量発注方式は、“発注点方式”とも呼ばれており、発注点を設定して在庫を管理する方式です。
適切な在庫量を定めて、在庫の補充が必要になったタイミングで発注を行うことで、過剰在庫・欠品が発生するのを防止できます。ただし、発注時期が定まっていないため、急な需要の変化には対応できないケースもあります。
定期発注方式は、事前に設定した期間に自動で発注を行う方式です。
発注するタイミングを月初・月末、2ヶ月に1回などに決めます。発注業務の負担を軽減できる一方で、発注量が定められていないため、在庫数や需要を正確に把握していなければ、過剰在庫・欠品が生じやすくなります。
発注点の計算方法
発注点を設ける際は、定量発注方式で算出します。基準となる発注点の算出には、次の計算式を用います。
▼発注点の計算式
発注点=1日の平均出荷量×調達期間+安全在庫 |
たとえば、商品の1日の平均出荷量が100個、調達期間が7日間、安全在庫が50個の場合、発注点は750個となります。
▼計算例
100個×7日+50個=750個 |
このケースでは、在庫数が750個を下回ったときに商品の発注が必要と判断します。発注点を明確に設定することで、過剰在庫を抱えたり、在庫不足に陥ったりするリスクを軽減できます。
以下では、発注点の計算に必要となる1日の平均出荷量・調達期間・安全在庫について詳しく解説します。
1日の平均出荷量
1日の平均出荷量とは、1日当たりの使用量や販売量の数量を指します。
商品を発注する際は、リードタイム(※)が発生するため、その期間中にも在庫は減少します。1日の平均出荷量を把握しておくことで、在庫が十分に確保されている状態で発注できるようになり、欠品を防止できます。
また、出荷速度(消費速度)が速い場合には、最大値または中央値を用いたほうがよいケースもあります。自社商品の特性に応じて検討することが重要です。
※リードタイムとは、発注から納品に至るまでの生産や輸送などにかかる時間のこと。
調達期間
調達期間とは、発注してから納品されるまでの日数のことです。材料の場合は発注リードタイム、仕掛品の場合は生産着手から完了までの製造期間を指します。
調達期間を把握することで、発注期間中の欠品を防げるほか、出荷量の変動にも対応できるようになります。調達期間も、1日の平均出荷量と同様に自社商品の特性に応じた設定が必要です。
安全在庫
安全在庫は、需要変動が生じた際の欠品を防ぐうえで最低限必要になる在庫量を指します。需要変動には、季節性や流行などによる需要の変化に加えて、リードタイムの変動も含まれます。
特に、商品の需要や出荷速度の変化が生じやすい商品は、安全在庫を把握しておくことが重要です。
発注点を管理する際の3つのポイント
発注点を管理するポイントには、以下の3つが挙げられます。
- 在庫数を正確に把握する
- 需要状況に応じて発注点を見直す
- システムを活用する
1.在庫数を正確に把握する
発注点を適切に管理するには、在庫数を正確に把握することが重要です。
複数の担当者が在庫を管理する際、管理方法にばらつきがあると、在庫数を正確に確認できず発注点を正しく算出できません。実在庫とのデータの差異を防ぐために、在庫管理の方法を統一したり、棚卸を行ったりする必要があります。
在庫の適正化には、自動で通知される受発注システムを導入するのも有効です。竹田印刷の『TS-BASE 受発注』なら、商品単位の発注点設定、在庫数が発注点を下回った場合にメールで通知するなどの機能が備わっています。
導入事例はこちらからご覧ください。
2.需要状況に応じて発注点を見直す
需要状況に応じて発注点を見直すことも重要なポイントです。
季節性によって需要が変動する商品の場合には、季節ごとに発注点を再設定します。また、過去の実績データや社会情勢を踏まえて定期的に需要予測を行うことで、管理の精度を高められます。
3.システムを活用する
在庫の管理や需要予測をより正確かつ効率的に行うためには、システムを活用することも有効です。
実在庫の把握をはじめ、過去データを用いた発注点の計算、発注点の再設定などができるシステムを活用すると、効率的に発注点を管理できます。
発注点の管理を含めて、受発注業務を一元管理できるシステムであれば、業務の効率化も図れます。
発注点の管理については、こちらの記事で詳しく解説しています。
受発注システム活用で在庫管理を効率化!
発注点を用いた在庫管理では、在庫状況の把握だけでなく、リードタイムや需要に応じた安全在庫などを考慮する必要があります。より効率的に在庫管理業務を行うには、受発注システムの活用が有効です。
『TS-BASE 受発注』は、受発注に関わる業務を一元管理できるシステムです。倉庫管理システム(WMS)の機能と注文の仕組みを兼ね備えたシステムで、発注点の管理を一つのシステム内でフォローできます。
商品単位ごとに発注点設定をできるほか、在庫数が発注点を下回った場合にはメールで通知されるため、発注漏れを防げます。また、指定期間での総出荷数をボタン一つで資料化して、平均出荷量や調達期間を検討する際にも役立ちます。
そのほか有料オプションとして、注文数・出荷数と在庫数から、残りの注文可能週数(日数でも算出可)を自動計算するデータ分析機能があります。
詳しくは、こちらをご確認ください。
なお、在庫管理の課題については、こちらの記事で解説しています。併せてご覧ください。