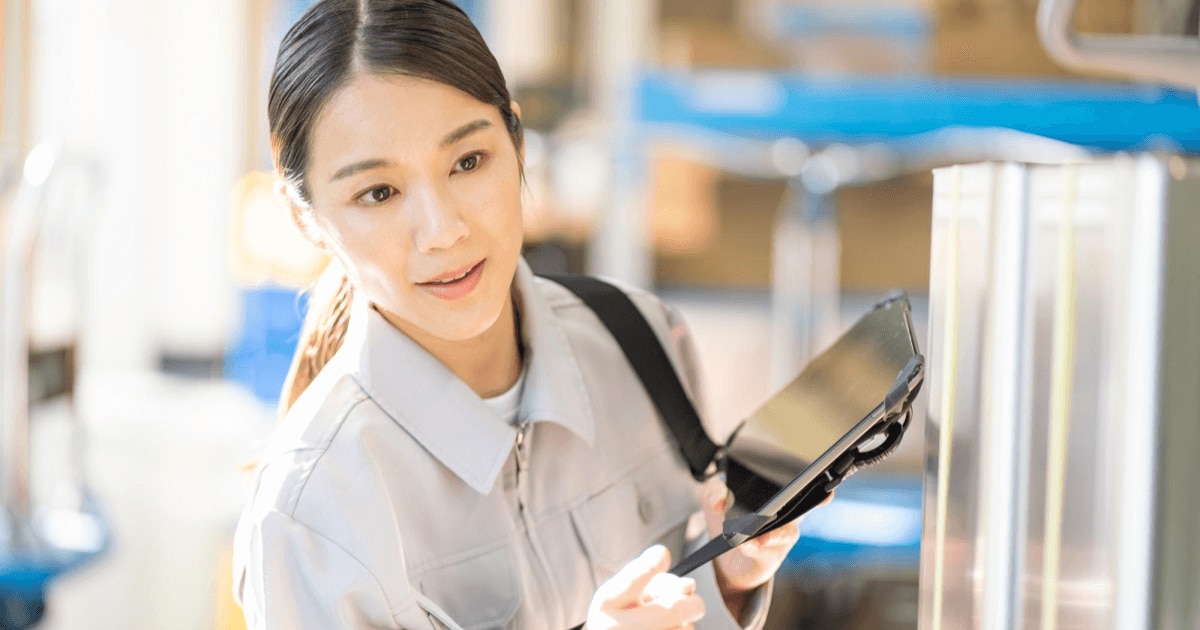
リードタイムとは? 種類や計算方法、短縮のポイントについて解説
業務の工程管理に用いられる単位に“リードタイム”があります。
収益や生産性を向上するためには、できるだけリードタイムを短縮することが望まれます。「自社においてどのようなリードタイムを把握しておく必要があるのだろう」「どのように計算すればよいのだろう」と疑問を持つ担当者さまもいるのではないでしょうか。
この記事では、リードタイムの概要をはじめ、一般的な種類や計算方法、短縮のポイントなどについて解説します。
目次[非表示]
- 1.リードタイムとは
- 2.リードタイムの種類
- 2.1.1.開発リードタイム
- 2.2.2.調達リードタイム
- 2.3.3.生産・製造リードタイム
- 2.4.4.配送リードタイム
- 3.リードタイムの計算方法
- 4.リードタイムを短縮するポイント
- 5.TS-BASE 受発注で配送リードタイムの削減を実現
リードタイムとは
リードタイムとは、ある工程の始まりから終わりまでにかかる時間・期間のことです。業種によって対象とする時間・期間は異なりますが、一般的には短いほうがよいといわれています。
“リードタイムが短い”というのは、効率的な業務を行うことができていて、最終的な納期を早められるということです。そのため、顧客満足度の向上や販売・受注機会の拡大などのメリットが期待できます。
なお、混同されやすいものに“納期”がありますが、リードタイムは一定の日数を指すのに対して、納期は顧客に納品する期限を指します。取引のトラブルを防ぐためには、リードタイムがどれくらいかかるのかを算出して、問題なく納品できる日に納期を設定することが重要です。
リードタイムの種類
業種や業務内容によって対象期間は異なりますが、一般的なリードタイムには次の4つが挙げられます。
1.開発リードタイム
開発リードタイムは、製品の企画立案から開発、製造までにかかる期間を指します。市場・トレンド調査や競合調査、製品の企画立案、製造から出荷までのプランニング、図面の作製、試作などの工程が該当します。
2.調達リードタイム
調達リードタイムは、製品の生産・製造に必要な原料・部品を発注して、納品されるまでの期間のことです。原料・部品の選定や調達先の決定、発注に加えて、輸送・搬入までの期間、受け入れに要する期間なども含まれます。
3.生産・製造リードタイム
生産・製造リードタイムは、原材料の加工から製造、完成品の出荷までにかかる期間を指します。製品の生産・製造に着手してから製品が完了するまでのすべての工程が含まれます。
4.配送リードタイム
配送リードタイムは、工場や倉庫にある製品の出荷指示があってから発注先に納品するまでの期間のことです。出荷リードタイムや物流リードタイムなどと称されることもあります。倉庫での出荷指示や準備、トラックによる輸送などの工程が配送リードタイムに該当します。
配送リードタイムについては、こちらの記事でも解説しています。
リードタイムの計算方法
リードタイムの計算方法には、主にフォワード法とバックフォワード法の2つがあります。ここからは、それぞれの計算方法について解説します。なお、リードタイムは会社の営業日(休業日を含まない)で計算することが一般的です。
フォワード法
フォワード法とは、着手日を起点として工程ごとにかかる日数を明らかにして、完了までの全体的な日数を計算する方法のことです。
各工程にかかる日数を見積もり、並行して着手できる工程は重複してカウントします。例えば、生産・製造にかかる工程が3つあり、工程②③を並行して着手できる場合は、以下のようになります。
▼例:生産・製造にかかるリードタイム
この場合、生産・製造にかかる全体のリードタイムは、2日(工程1)+5日(工程2と3が含まれる)=7日となります。
フォワード法は、はじめに着手する日を決めたうえで、第1工程から順に計画していくため、工程1の開始日を早められることが特徴です。並行して作業が必要な場合や、急ぎの納品依頼があったときなどに適しています。
バックフォワード法
バックワード法は、納品日から逆算して、各工程にどの程度の日数を充てられるのかを計算する方法です。納期や出荷予定日などの最終工程を起点として、遡って所要日数を見積もります。
例えば、生産・製造にかかる工程が3つあり、最終工程の期日が6/14になる場合のリードタイムは、以下のように計算します。
▼例:生産・製造にかかるリードタイム
この場合、リードタイムは2日(工程1)+3日(工程2)+5日(工程3)の10日となります。
フォワード法とは異なり、各工程の着手日や作業日が重ならないように設定できるため、余裕のあるスケジュールが組めることが特徴です。ただし、各工程で何らかのトラブルが発生した場合には、納期に遅れる可能性があります。
納期があらかじめ決まっているときや、並行して作業できない工程の場合に適しています。
リードタイムを短縮するポイント
業種や対象期間によってリードタイムの短縮方法は異なりますが、共通するポイントには、次の2つが挙げられます。
▼リードタイムを短縮するポイント
- 非効率な業務フローを見直す
- ミス・手戻りをなくす
業務フローを可視化して、労力・時間がかかっている業務の手順や作業方法を見直すことで、業務の効率化につながります。
例えば、配送リードタイムを短縮したい場合、受注方法を統一したり、電話・FAX・メールでの受発注をデジタル化したりして、取引先とのやり取り回数を減らす方法があります。
また、ミスや手戻りによるロスを防ぐために、担当者の業務を標準化する、情報共有ができる仕組みを作る、システム活用によって自動化を図ることも有効です。
なお、配送リードタイムの削減を実現した事例を以下の記事で解説しています。
さらに、販促物の管理方法を見直したい場合は、こちらの資料も参考にしてみてください。
▼販促物の管理、できていますか?管理不足が招く問題と解決策の教科書
TS-BASE 受発注で配送リードタイムの削減を実現
業務の工程管理に用いられるリードタイムは、一般的に短いほうがよいとされています。リードタイムを短縮するには、非効率な業務フローを見直すこと、ミス・手戻りをなくすことがポイントです。そのためには、システム活用によって自動化を図ることも一つの方法です。
受発注システムの『TS-BASE 受発注』では、受発注業務のデジタル化によって配送リードタイムの短縮を後押しします。在庫管理や入出荷管理などの物流に関する機能も備わっているため、受発注に関わる業務の改善にも貢献します。また、受発注システムとWMS(Warehouse Management System:倉庫管理システム)が一体化しているため、情報の連携も容易に行えます。
配送リードタイムの短縮や受発注業務の効率化にお悩みの方は、TS-BASE 受発注がおすすめです。サービスの詳しい内容は、こちらからご確認ください。